Just How Welding Examination Contributes to Longevity and Integrity in Construction Jobs
Welding examination acts as a fundamental component in making sure the long life and integrity of fabrication tasks. By systematically determining prospective issues during different stages of production, welding examinations not just prevent costly failures yet likewise promote a culture of quality control within the team. Utilizing innovative techniques, such as non-destructive testing, promotes comprehensive examinations while preserving product integrity. As jobs progress, the impact of these inspections becomes increasingly noticeable, increasing vital inquiries regarding their long-lasting benefits and ramifications for overall job success. What particular methods can be implemented to maximize these benefits?

Relevance of Welding Inspection
Making certain quality via welding evaluation is a vital part of any type of manufacture job. It acts as a guard to confirm that welding procedures meet recognized requirements and specs, therefore enhancing the overall integrity of the framework or element being fabricated. Welding evaluation is not simply a procedural step; it is an essential practice that helps identify possible concerns early, making sure that they are attended to prior to they escalate into substantial troubles.
The value of welding evaluation can be underscored by its role in keeping security and sturdiness. Welded joints are often based on extreme problems, and any type of problems can endanger the efficiency and longevity of the end product. By implementing strenuous evaluation protocols, companies can guarantee conformity with market regulations, consequently reducing threats related to structural failings.
Moreover, efficient welding inspection cultivates confidence amongst stakeholders, including clients and governing bodies, that the job meets the highest possible high quality criteria. This not only boosts the reputation of the maker but likewise adds to long-lasting expense savings by preventing rework and possible liabilities. Eventually, welding examination is integral to the success and integrity of fabrication tasks, reinforcing the value of quality control in engineering methods.

Usual Welding Defects
Welding defects can considerably undermine the structural integrity of made parts, making their recognition and correction vital. Typical welding flaws can be extensively categorized into 3 kinds: geometric, metallurgical, and service-related.
Geometric flaws consist of problems such as undercutting, where the base metal is eroded at the side of the weld, and too much convexity, which can cause anxiety concentration points. These issues can endanger the stamina and sturdiness of the weld joint.
Metallurgical problems arise from inappropriate welding treatments or materials, bring about troubles such as porosity, where gas pockets develop within the weld, and lack of blend, which happens when the weld metal falls short to bond correctly with the base metal. These concerns can considerably weaken the weld's performance.
Service-related flaws may not come to be obvious till after the element remains in use. Instances include cracking because of thermal stress or exhaustion, which can result in tragic failures otherwise dealt with.
Recognizing these typical issues encourages producers to implement efficient evaluation strategies that improve the integrity and durability of their tasks, ultimately making sure safety and performance criteria are fulfilled.
Evaluation Strategies and Methods
A comprehensive method to examination techniques and methods is necessary for identifying and reducing welding defects in construction jobs. Numerous approaches are used to ensure the integrity of welds, including aesthetic examination, ultrasonic screening (UT), radiographic screening (RT), magnetic particle testing (MT), and dye penetrant testing (PT) Each technique has its staminas and certain applications.

Magnetic fragment testing is helpful for spotting surface area and near-surface problems in ferromagnetic products. By applying a magnetic area and using ferrous bits, inspectors can determine discontinuities properly. Lastly, color penetrant screening highlights surface-breaking problems via the application of a dye that leaks right into cracks, making them visible under ultraviolet light.
Utilizing a mix of these methods makes sure a strenuous analysis, boosting the reliability of welded frameworks.
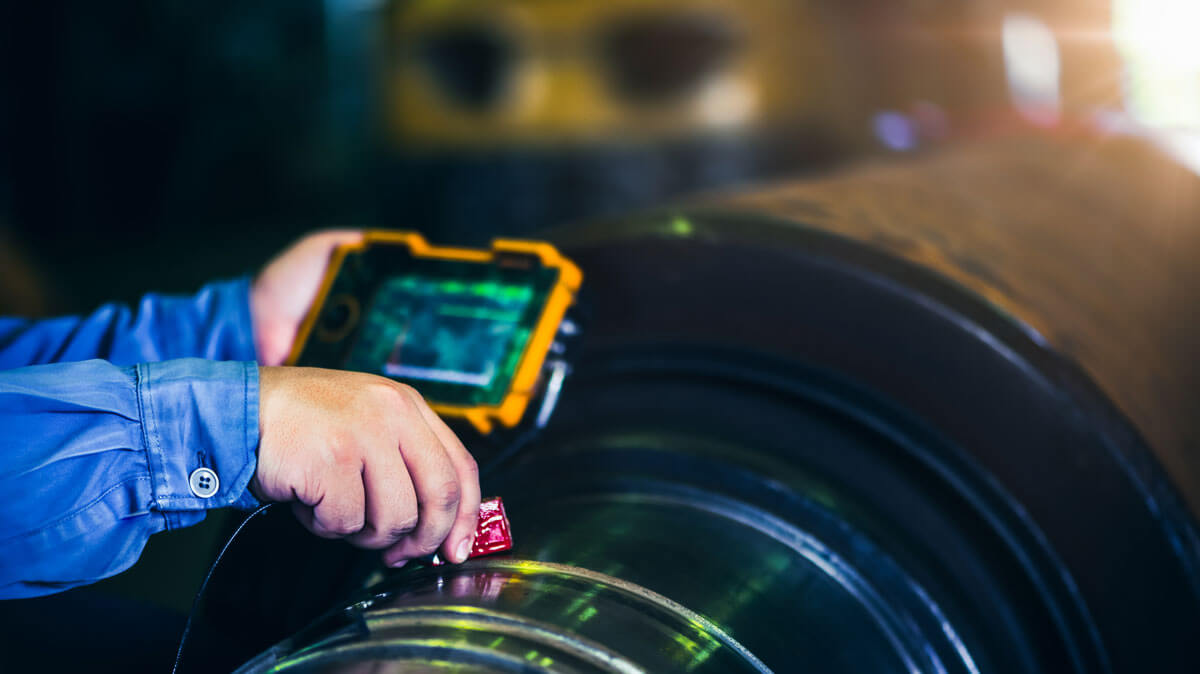
Impact on Project Longevity
Effective inspection techniques dramatically affect the durability of construction projects. By identifying possible flaws and variances in welding processes, evaluations ensure that frameworks are developed to endure operational stresses with time. When welds are completely analyzed, the likelihood of unseen problems, which might lead to architectural failures, is decreased.
Routine evaluations browse around this site promote adherence to market standards and laws, which are important for guaranteeing the durability of bonded joints. Such compliance not just enhances the stability of the More Bonuses project yet likewise comforts stakeholders pertaining to the quality of the work. In addition, timely discovery of problems permits for restorative activities to be taken early, avoiding pricey repair work or full overhauls down the line.
In addition, effective assessment techniques foster a society of quality control within construction groups. When employees know that their job will certainly be carefully reviewed, they are more probable to abide by ideal practices and preserve high requirements throughout the manufacturing process. Eventually, this commitment to high quality not just expands the life-span of the task but also decreases maintenance expenses, thus improving the general financial feasibility of manufacture undertakings.
Enhancing Dependability in Construction
Dependability in fabrication is significantly enhanced via strenuous assessment processes that address possible weak points in welding practices. Effective welding inspection not just recognizes flaws early but additionally supplies vital feedback to welders, ensuring adherence to developed requirements and requirements. By utilizing non-destructive screening methods, such as radiographic or ultrasonic assessments, fabricators can identify the stability of welds without compromising the product.
Additionally, regular assessments foster a society of quality and liability among manufacture teams. When welders recognize that their work undergoes strict examinations, they are more probable to adhere to finest practices and procedures. This proactive technique decreases the risk of expensive failings throughout the operational phase of a job.
In addition, comprehensive documents of examination results creates a useful database of details that can be used for future projects. Patterns in flaws can be assessed to improve welding techniques and training programs (Welding Inspection Milwaukee). Eventually, improving integrity in manufacture through extensive assessment refines not just raises the lifespan of the fabricated components but additionally enhances stakeholder confidence in the job's general top quality and durability. Purchasing robust welding evaluation methods is vital for accomplishing long-lasting dependability in any type of construction venture.
Conclusion
In recap, welding assessment serves as a vital part in making sure the durability and reliability of manufacture jobs. By identifying issues early and utilizing non-destructive testing approaches, assessments foster a society of high quality assurance that follows industry criteria. The systematic documents of results not just assists in trend evaluation but additionally enhances liability and structural honesty. Ultimately, reliable welding evaluation techniques reinforce stakeholder self-confidence and considerably add to the economic feasibility of fabrication ventures.
Welding inspection serves as a fundamental component in ensuring the longevity and dependability of manufacture tasks.Ensuring quality with welding assessment is a critical component of any type of construction job. Inevitably, welding examination is integral to the success and reliability of fabrication projects, reinforcing the worth of high quality guarantee in engineering methods.
A detailed technique to examination strategies and approaches is crucial for recognizing and minimizing welding issues in manufacture tasks.In recap, welding assessment serves as an important component in ensuring the long life and integrity of construction jobs.